Medio siglo de tradición en la fabricación de tubos plásticos;
Entrevista al Sr. Carlos Gutiérrez, director de Plastiducto
Volver a Entrevistas
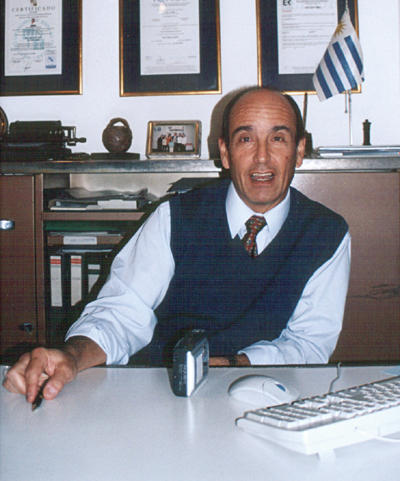
Sr. Carlos Gutierrez, Director de Plastiducto S.A.
En cincuenta años de existencia, y sobrellevando las más difíciles crisis del país y la región, Plastiducto ha sido un referente del Uruguay en el rubro de tuberías plásticas.
Plastiducto nace en 1956 como empresa distribuidora de los primeros tubos que se fabricaron en el país, por una industria especialmente creada para ese proyecto, por dos reconocidas empresas del sector, Plastisur S.A. y Gutierrez y Richarson, fundada en 1947, socia fundadora en 1956 de la antigua Cámara de Moldeadores de Plásticos, la actual AUIP. El fin era el desarrollo industrial de un producto innovador en el mercado, ya que no existía la producción local de tubos de polietileno. Pocos años después de esta alianza, en 1961, se separan ambas empresas. En el año 1970 se separa una rama de la empresa aplicada a inyección, que hacía básicamente artículos de laboratorio, y a partir de ese momento Plastiducto continúa, ya no como distribuidora, sino como empresa industrial. Comienzan los nuevos desafíos, principalmente como incursionar en los tubos de gran diámetro. Fabricar por los años 70, diámetros de 1 metro, era algo muy novedoso para la época. Lógicamente la coyuntura de ese momento favorecía la producción de estos artículos, porque había un dólar barato y mano de obra cara, en consecuencia el producto de plástico podía sustituir bien a productos tradicionales como el hormigón, que eran los habitualmente utilizados. Un ejemplo de las ventajas, es que para hacer 8 metros de pase se utiliza un solo tubo de PE, que lo podían transportar 2 hombres, en cambio con hormigón se necesitaban 8 tubos movidos por una grúa y demás complicaciones. Era realmente un producto que iba a simplificar, frente a la mano de obra implicada en la fabricación y la instalación de un tubo de hormigón. Y así tomamos este producto como una bandera para nuestro desarrollo, pero hasta el año 1982, período en que Uruguay entra en una fuerte crisis, debido a la caída del plan oficial de control del mercado cambiario, la conocida “Tablita”, en el que el dólar se duplicó de un día para otro, y nos obligó a discontinuar la producción de tubos de grandes diámetros, por caer la demanda. A partir de allí cambiamos nuestro sistema de fabricación, en vez de hacerlos enrollados por sistema helicoidal, los empezamos a hacer por extrusión directa, y así hasta el día de hoy. Es muy interesante analizar la evolución de nuestra empresa, ya que acompaña en forma de espejo la situación nacional. Estamos directamente asociados a la suerte de la producción en el país, tanto la construcción, el agro, como la industria en general, por eso pienso que observar a Plastiducto es estar observando la evolución de la economía del país, especialmente en momentos de crisis.
¿Cuáles son las principales áreas de aplicación de sus productos?
Nuestros productos están orientados principalmente al mercado agropecuario, la industria y la construcción. En un inicio fué el agro ampliamente receptivo, y nuestro tubo se convirtió en el producto por excelencia. Posteriormente fue adoptada la utilización de nuestros tubos por OSE (Obras Sanitarias del Estado), para hacer lo que ellos llamaban los ramales de emergencia para la red de agua. Que en realidad eran instalaciones con un sentido de emergencia, aunque podían ser perfectamente instalaciones definitivas. Lamentablemente no las instalaron con este concepto. En tuberías logramos fabricar con gran eficiencia grandes diámetros, que hemos desarrollado gradualmente con el tiempo. En el año 70 fabricábamos diámetros de hasta 4 pulgadas, 100 mm. A partir de los años 80 ya estábamos en 200 mm., por el año 86 estábamos en 400 y en el 93 hacíamos 800 mm. Siempre nos fuimos aventurando a ir aumentando progresivamente el diámetro del tubo fabricado, en una forma exponencial. Y así llegamos al día de hoy, con una línea bastante importante de productos, basados principalmente en poliolefinas, Polipropilenos, Polietilenos tanto de alta como de baja densidad. Cuando empezó la producción de Plastiducto fuimos los primeros fabricando los tubos de polietileno, y cuando el tubo de PVC incursionó en el área de la construcción, fuimos la primera empresa en tener la aprobación para fabricar los tubos en el sector de sanitaria.
Lamentablemente el rubro se presta para la utilización de materiales recuperados y reciclados. Entonces en ese sentido, se quedó un poco tergiversada la idea de un tubo de plástico de un alto compromiso técnico, y no se van a tener los resultados que se pretendían de la imagen del tubo del polietileno. Por eso hay que tener mucha precaución, sobre todo con la utilización de un producto sin garantía de calidad.
Tenemos un orgullo particular, que es el reconocimiento de la gente cuando se refieren a un tubo de plástico en el Uruguay, lo nombran Plastiducto, el de las “tres líneas”, como las grandes marcas asociadas a un producto determinado.
¿Porqué las tres líneas?
Cuando empezamos la fabricación de tubos los sistemas de impresión y grabado no estaban muy desarrollados, era todo más complicado y hacer una marca que fuera visible o identificable era difícil. Por otra parte la norma dice que una marca aplicada debe ser indeleble e ilegible. Por eso desarrollamos las líneas que no eran legibles, pero sí asociaban a un fabricante, como a veces se asociaba marcas deportivas.
Anteriormente el sistema en el cual se fabricaba el tubo era mediante la calibración por un mandril, por el lado interno del caño, por su diámetro interior. Cuando el sistema de producción cambió a sistemas de vacío o de tapón, la calibración se hacía por el exterior, entonces lo que contaba era la parte externa. Pero como al principio la calibración era interna, nos quedaba la parte externa libre. Entonces había una solución muy fácil e ingeniosa para hacer una marca indeleble e ilegible, que era hacerle unas pequeñas ranuras a la hembra, a la salida de la matriz, entonces el material fluía por esas ranuras y salían automáticamente las líneas sobre relieve. Cuando teníamos un tubo sobre una franja que estaba inundada y queríamos saber si esa rotura había sido de un tubo plastiducto, simplemente colocando la mano por bajo del agua y buscando al tacto las líneas sobre relieve era el mejor sistema de identificación. Hoy día las tres líneas son de colores para la identificación de nuestros tubos, y están coextrudadas, codificando el uso del tubo de PE.
¿Respecto a la exportación?
Estamos exportando dentro del área, Argentina, Brasil y también a Bolivia. Podemos decir con orgullo que en Bolivia tenemos más de 400 kilómetros de redes de gas urbano instalado. Tuvimos exigencias importantes para ingresar a este mercado, y gracias a nuestra certificación ISO 9001 2000 para el sistema de gestión, los ensayos del producto terminado del LATU, la certificación del fabricante del material, y por supuesto la calidad de producto, logramos ingresar al mercado boliviano y realizar tan importante tendido de redes de gas. Entramos de la mano de Georg Fiscischer, empresa suiza de más de 200 años pionera en la tecnología de los accesorios que acompañan las redes de gas y de agua, accesorios de electrofusión. Fue con ellos que introdujimos los tubos plastiducto junto a sus accesorios en Bolivia. Para fabricar un buen tubo de plástico para gas, además de que hay que tener una alta tecnología, el 90 % de los ingredientes se resumen en una sola palabra; “escrúpulos”, para que ese tubo sea fabricado con el material adecuado para el fin que se plantea. “En agua una pérdida es irrigación, en gas es explosión”. Los requisitos son otros y los cuidados que hay que tener son otros.
En el caso de las soldaduras de redes de nuestros tubos, si bien no nos compite el tema, hemos hecho tanto en Uruguay como en Bolivia, en varias oportunidades, seminarios de capacitación para los operadores de redes, tanto en el sistema de fusión a tope, como el de electro fusión. La dificultad en la exportación se crea cuando hay que suministrar el tubo en tramos de 12 metros y no en rollos de 100 metros, que es la gran ventaja del tubo de polietileno, ya que no tiene uniones. Esto sucede cuando tenemos diámetros que superan los 90 milímetros, los rollos tomarían un diámetro tan grande que no podríamos transportarlo en un camión común de carga. Hay que pensar en tramos rectos para el transporte. Esa es la limitante. También los tubos de grandes diámetros, tienen una dificultad en la exportación que es la alta incidencia del flete. Pensando en el mercado de Bolivia, existen proyectos para transformarse en uno de los principales exportadores de gas, y para estos proyectos, hablamos de tuberías a gran escala. El problema que se suscita aquí, es que están incursionando en el mercado los países asiáticos, caso los chinos, que anteponen el crédito en primer lugar para colocar sus tubos y accesorios. En consecuencia, el cliente te pide primero la condición de crédito para vender, entonces no se está vendiendo un producto sino, se está vendiendo un crédito. Y esas son las dificultades, que en estos tiempos nos estamos encontrando, no competimos contra industrias, sino contra bancos.
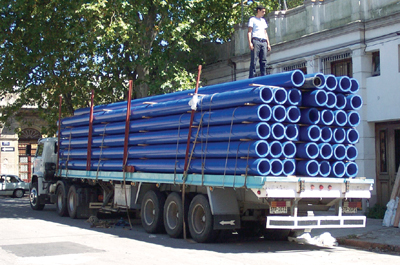
¿Está desarrollado el mercado uruguayo?
Cuando vemos que en Europa los operadores de agua y gas manejan redes de PE, es por una sencilla razón, no se pueden darse el lujo de tener pérdidas. En nuestro país no podemos permitir que las redes de distribución no sean confiables, y perder en altísimo porcentaje el agua corriente. Cuando se compra tuberías, hay que evaluar no solamente el crédito a largo plazo, sino que en ese largo plazo no se producen deterioros en las redes y aumentan considerablemente los costos. Por eso hay que invertir mejor, y esto es un tema grave que ocurre y puede ocurrir. Generalmente cuando hay una licitación de tuberías, lo primero que hacen es comparar los tubos en precios y condiciones, sin evaluar los temas de calidad que pueden producir esas consecuencias terribles para la ciudad. En la medida que no se cambie el criterio en forma profunda de la evaluación del producto y del costo real, en su aplicación y amortización en los 50 años de expectativa de vida útil que tiene, vamos a seguir invirtiendo mal nuestros dineros y nuestros recursos en malos proyectos. La red se está haciendo de plástico pero mayoritariamente en PVC, que comparativamente material con material, resulta más barato. Pero no es más económico en el uso final. Porque es un tubo que para instalarlo viene en tramos de 6 metros, mientras que el PE viene en rollos. Cada 6 metros hay que hacer una unión de goma, que puede ser un problema, puede haber roturas con raíces de árboles, pueden ocurrir vacíos en la red y el agua contaminada de la napa freática filtre por esas gomas. Cosa que no ocurre con el PE porque es todo soldadura, no se corren riesgos de roturas. Es significativo ver los equipos de reparación que se necesitan en las redes. Por ejemplo, en Brasil, la ciudad de Porto Alegre basa sus redes de agua en acero y polietileno. El 30% de las redes son de PE, el resto de acero. Para atender ese 30 % de las redes, tienen un solo equipo de reparación. Para atender el 70 % de las redes de acero, tienen 20 equipos de reparación. Si vemos en Uruguay, que todavía hay redes de fibrocemento, para darte un ejemplo, con el solo costo de reparación de una fuga, se podría hacer toda una cuadra de PE y hacerla confiable por 50 años. Los técnicos de los organismos públicos se dan cuenta de esta situación. Quizás los pliegos, las condiciones de la licitación son los que determinan que al final deban comprar el producto más barato, porque están admitidas en las redes como válidos. El PE se utiliza en los países que tienen movimientos sísmicos, es decir es antisísmico, ya que hasta las de acero quiebran. Estoy confiado en que la apuesta que hemos hecho a las poliolefinas, va a ser el futuro, se va a ir decantando. El otro producto que nos da soporte es el polipropileno, para instalaciones domiciliarias de aguas fría y caliente, tanto en la versión roscable como la fusionable, es nuestro caballito de batalla, que es lo que se vende en forma masiva, y le da estabilidad a la empresa. Por eso es muy importante el respaldo del mercado interno.
Fabricamos productos muy técnicos, multicapas, donde podemos obtener diferentes características de un producto. Por ejemplo, tubos para barreras para el oxígeno, impermeables, resistentes al sol, resistentes a la temperatura, en fin, con un alto grado de especialización, lo que da una aplicación en ciertos nichos del mercado, en una alta gama de especificaciones técnicas, como lo son la calefacción, puestos de gasolina, transporte de combustibles, etc.
Por eso invertir correctamente desde un inicio es lo fundamental, o lo hacemos bien, o seguimos gastando dinero mal invertido.
9 de Junio de 2006 / Montevideo - Uruguay
Volver a Entrevistas
|