Un grande de la Industria del Plástico de Latinoamérica;
Entrevista a Abel Hofman, fundador de NIBO PLAST
Volver a Entrevistas
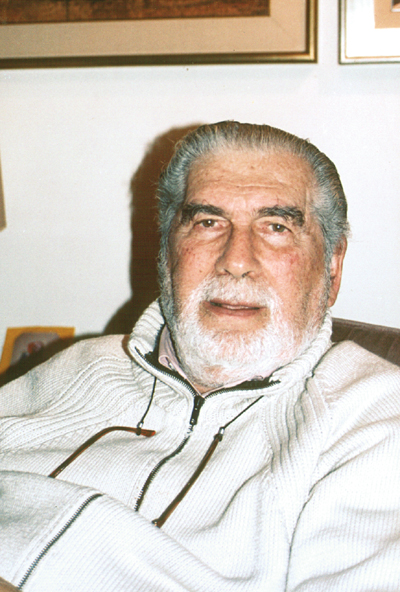
Sr. Abel Hofman, Fundador y Director de NIBO PLAST, 1952-1999.
Primer Presidente de ALIPLAST (Asociación Latinoaméricana de Industrias del Plástico) 1966 - Reelecto 1967.
Nacido en la ciudad de Buenos Aires, en el año 1929, Abel Hofman, llegó como un joven emprendedor al Uruguay, para fundar una de las empresas pioneras en el mercado de Plásticos; NIBO PLAST. Pionero en varios rubros de transformación de plásticos, socio fundador de la Asociación Uruguaya de Industriales del Plástico, AUIP, y fue el primer presidente, por dos períodos consecutivos, de ALIPLAST (Asociación Latinoamericana de Industrias del Plástico) fundada en 1966.
En mayo del año 1952, vine al Uruguay, en compañía de mi suegro y mis cuñados, con la idea de formar una pequeña fabriquita para la industrialización de planchas de acrílico. En ese entonces, en el Uruguay las planchas las importaba la compañía Duperial, una conjunción de dos empresas monstruos de la época, Dupont e ICI (Imperial Chemical Industries). Cuando hablo del desarrollo de acrílicos, hay que entender que en aquél entonces no se transformaban por los métodos tradicionales actuales, era simplemente por calor y presión que la hacía un chorro de aire sobre un molde hembra, proceso por deformación. Y así comenzamos a fabricar unas bandejas con el ferviente deseo de poder sustituir las que se utilizaban en las heladeras, que eran de hierro esmaltado. El problema de estas bandejas, es que con un golpe se saltaba el esmalte y quedaba un centro permanente bacteriológico. En realidad no sabíamos como motivar el cambio, teníamos el conocimiento técnico para fabricar la bandeja, pero no como hacer para venderla. Hacíamos, en un mercado muy limitado, unas bandejitas de acrílico muy lindas, que las vendíamos para el revelado fotográfico, un material muy noble y bastante resistente. Queríamos vender a las empresas grandes, principalmente a General Electric, quienes fabricaban de 15 a 18 mil heladeras por año. No recuerdo como fue que hicimos para conseguir una entrevista personal con el presidente de la compañía General Electric, don Emilio Elena, pero la cuestión es que la tuvimos. La razón de la visita era convencerlo de sustituir la bandeja tradicional de las heladeras, por el plástico, un producto novedoso, revolucionario, irrompible, y con una cantidad de virtudes que en esa época se desconocían. En el curso de la reunión y entre las argumentaciones que yo esgrimía, además de la belleza, su practicidad, fundamentalmente no se rompía, cosa que le pasaba al esmaltado. Para mostrarle realmente que lo que yo decía era cierto, desenvolví el paquete que tenía la bandeja, la tiré con fuerza al piso y… sorpresa!, se hizo mil pedazos. La bandeja se rompió, y yo quedé paralizado. No recuerdo que cara habrá puesto el Sr. Elena, no podía mirarlo, todos mis argumentos se me caían. No sabía que hacer, hasta que él con mucha tranquilidad salió del paso diciéndome; -“¿Cuánto decía Ud., que valía esta bandeja?”. Yo ni me acordaba cuanto valía, no se el precio que le dije, pero debería ser más o menos el correcto, y entonces me afirma: -“vamos a empezar comprando 5.000.”
Yo no sabía que contestarle, y le pregunté; -“discúlpeme, la bandeja se rompió, pero no se rompen… ¿Por qué es que me compra la bandeja?”, a lo que me contesta - “Le compro la bandeja porque no se rompe, si la bandeja se rompiera, realmente usted no la hubiera tirado con la firmeza con que la tiró, me hubiera dicho que no se rompe, pero no la hubiera tirado, usted está convencido de que no se rompe.” En realidad no se lo que pasó, porque esa bandeja no debía romperse, pero ahí se rompió. Y esa fue la razón por la cual me hicieron el primer pedido de bandeja y fue el principio del desarrollo de nuestra fábrica y del moldeo de planchas de acrílico.
¿Cómo viviste el desarrollo del plástico?
La evolución del plástico en el Uruguay no fue muy diferente de lo que fue en el resto del mundo. Si bien año a año íbamos creciendo en el país, en el resto del mundo crecía y evolucionaba más rápidamente que nosotros, y con los años se hacen las diferencias. El sector de plásticos de la década del 50 era muy incipiente. Existía en Paysandú, una empresa dedicada a termofijos, que era la empresa Olivera y Cia, que fabricaba en aquel entonces aparatos de radio en bakelita. Estaban Pinto y Athías, otra empresa que fabricaba artículos de inyección, y ATMA, que era la principal en ese momento. El crecimiento es muy grande y muy rápido, pero a mi entender el gran desarrollo se da al final de la década del 50, cuando se empieza a fabricar film de polietileno y empiezan las tuberías y los caños de PE de baja densidad. A partir de aquí el desarrollo es mucho más rápido y acelerado. En la década del 60 fue muy avasallante, como una explosión, y las ferias internacionales abrieron los ojos a todas las posibilidades que había internacionalmente. Las principales ferias del plástico estaban en Europa, en Alemania, Italia, Inglaterra y Francia. Comencé a visitarlas, y me permitió abrir un campo muy grande en el conocimiento de las cosas que se iban desarrollando. En esta década, del 60, se comienzan a sustituir los materiales tradicionales por el plástico, lo que se hacía en hierro, aluminio y otros materiales, se empezaba a hacer en plástico. En la década del 70, que se abren las importaciones a nuevas tecnologías, es un poco la etapa de oro, donde empieza la gran creatividad.
¿Primer presidente de ALIPLAST?
En 1960 se formó la ALALC, como una institución con el objetivo de incrementar o desarrollar el mercado Latinoamericano. No se instaló como un ambicioso mercado común, sino simplemente como un sistema de intercambio de productos a los cuales se les iba a ir bajando aranceles. Con ella se forman las agremiaciones de empresarios de cada sector y cada uno de los gremios, formaron las agrupaciones latinoamericanas y así se formó ALIPLAST, Asociación Latinoamericana de Industriales del Plástico. Se decide la reunión en Montevideo, como todas las agremiaciones, porque Uruguay queda como sede, y se me elige primer presidente de ALIPLAST. Para el otro año, nuevamente se me elige presidente. Lamentablemente la ALALC no llega a nada, y con ella también cae esta primera versión de esta asociación. Recuero que los primeros 5 años fueron bastante activos, pero eso fue todo. Tal vez en los años que empezamos no era el momento y no era el lugar.
¿Cuál fue el desarrollo principal de Nibo Plast?
El fuerte desarrollo fué con el film de polietileno, cuando trajimos la primera extrusora en toda Latinoamérica, una Reifenhäuser. Al término de la guerra, ICI comienza a desarrollar conjuntamente con una empresa de maquinaria alemana, Reifenhäuser, un nuevo sistema de transformación para el polietileno, la extrusión soplada. Al film tubular de polietileno lo llaman pliofilm, y se fabricaba en el mayor secreto, todo un misterio. Así comenzó el desarrollo de la extrusión y del film de polietileno en el mundo, de manos de la ICI y Reifenhäuser. Por otra parte, la intención de ICI era comenzar a probar el producto en los mercados experimentales, y Uruguay era especial para ello. Paralelamente, mi suegro, el Sr. Niborsky, tenía un relacionamiento con ICI, y estas empresas vieron con agrado la posibilidad de comenzar con él, un desarrollo del nuevo producto en el sur. Empezamos a importar el Pliofilm por unos meses, vimos que era un éxito y automáticamente tanto Reifenhäuser como ICI, mancomunadas con nosotros, decidieron instalar en el país la primera máquina Reifenhäuser, una extrusora de 90 milímetros de diámetro y 11 diámetros. Eso era lo máximo de relación que tenía el tornillo de largo. Además hay que considerar que en aquel entonces, no existía más que un solo tipo de melt index en el PE que era grado 7, es decir se debía inyectar tanto una palangana como hacer un film extrudido, con ese melt index, por eso nunca llegábamos a espesores muy finos, cuarenta micrones era lo mínimo que podíamos lograr. El polietileno que usábamos se llamaba alkathene. El ancho de la máquina nos permitía hacer hasta 1 metro de ancho de film tubular. Y fué la primera máquina en toda América, desde México hasta el sur. Pero duró pocos años, en poco tiempo comenzaron a aparecer máquinas en todos los países, y el desarrollo de Reifenhäuser fue tremendo.
¿Cuál fue uno de los rubros más importantes de Nibo?
Nibo Plast incursionó por muchísimos rubros en la transformación de plásticos, como el caso de extrusión de PE, pero uno de sus rubros fuertes fue la inyección. Pero en realidad el gran negocio de Nibo, y de la mano de la inyección, fue la fabricación de moldes y el desarrollo del mercado interno con una variedad de productos que no existían. Si bien teníamos un parque de maquinarias para inyección muy importante y de grandes calibres, el tema moldes y su amortización en un mercado pequeño e incipiente como el uruguayo, eran un obstáculo a resolver. Entonces se nos ocurrió empezar a hacer moldes para exportación, basados en muestras que traíamos de Europa, que eran novedad en el área latinoamericana. Elegíamos un producto y fabricábamos el molde, para ello hacíamos una muestra de 4, 5 mil piezas que con ellas cubríamos el mercado local y luego con las muestras recorríamos América ofreciendo el molde, o bien en venta o alquilado. En muchos casos, se dio de hacer hasta 5 moldes iguales para distintos países. Llegamos incluso a vender en África. Por eso Nibo Plast, ante el asombro local, sacaba al año 6 ó 7 o más productos y sin costos de moldes, porque de esta forma salía amortizado para el exterior. Durante cinco años sacamos el primer premio al exportador de moldes del Uruguay, del Banco República. Llegamos a exportar 1,3 millones de dólares por año. Fué un rubro muy significativo.
También procesamos por ter moformado, soplado, realizamos extrusión de caños, teníamos equipos de vacumm forming, e incluso hasta hicimos pruebas con espumados. Respecto al film de polietileno que tuvo un auge muy grande y se desarrolló rápidamente desde el año 55, hasta el año 1961, año en el que apareció el primer competidor nuestro que fue Milprint. Hasta el año 62 estuvimos haciendo film de polietileno y después cometimos uno de nuestros errores, que fue dejar la venta directa, sólo lo hacíamos para nuestro propio uso. Otro rubro interesante que manejamos, fue el termoformado, para hacer grandes piezas para la industria de la refrigeración, donde también fuimos los primeros en desarrollarlo, de la mano con el desarrollo del poliestireno de alto impacto, HIPS. Trajimos el equipamiento y los moldes para la industria de refrigeración, y con el tiempo, en el país decae la industria, hasta que prácticamente desaparece y Nibo se quedó sin nada que hacer. Entre la década del 70 y la del 80, incursionamos en otros campos, como es por ejemplo, la fabricación de botones, de poliéster y la fabricación de las fichas para los casinos de nácar, donde teníamos controles muy estrictos de seguridad.
¿Como fue la última etapa de Nibo?
Acabábamos de construir una planta de 4 pisos en un predio de más de 4 mil metros, cerca de la fábrica que teníamos en ese momento, en la calle Chiávari. Esa nueva planta estaba dedicada especialmente a la terminación del producto, sobre todo de juguetería, uno de los rubros que exportábamos mucho. También funcionaba el depósito y almacenaje de los productos que fabricaba la empresa. El 28 de noviembre de 1978, habíamos tenido la visita del embajador de Inglaterra, y a las 12 y 35 del mediodía, luego que ya se había retirado, cuando la gente baja del cuarto piso a su descanso, cuatro muchachos se quedaron en el último piso y escondiéndose se pusieron a fumar. Entonces uno de ellos tira un cigarro encendido que calló sobre una lata de solventes. Se prendió fuego inmediatamente y como las estanterías eran todas de madera en aquél entonces, el fuego se propagó muy rápidamente. Ellos quisieron apagarlo pero no pudieron y en seguida ya estaba el cuarto piso en llamas. Cuando llegaron los bomberos no tenían agua suficiente, y la planta estuvo quemándose durante 24 horas. El mayor peligro que tuvimos, donde se concentraron los bomberos, fue donde teníamos un depósito subterráneo con aproximadamente unos 200 mil litros de combustible. Si tocaba el fuego, volaba la manzana, pero por suerte eso no ocurrió. Después de 24 horas se quemó todo. Los daños fueron tremendos. Eso marcó una línea en la vida de Nibo, antes del incendio y después del incendio. En ese año, el patrimonio de la empresa, era aproximadamente unos 10 millones de dólares. Teníamos 440 personas trabajando y producíamos unas 250 tons. con una facturación anual del orden de los 6 millones de dólares. Después del incendio se tomaron unas decisiones equivocadas, miradas en el tiempo, como por ejemplo, hacer caso al exhorto de la intendencia de no permitirnos reconstruir otro depósito en el lugar. Tomamos la decisión de salir a buscar una nueva gran planta que unificara todo, cuando teníamos que habernos quedado allí, y tener un crecimiento más pautado. El seguro pagó en aquél entonces los daños, algo así como 6 millones de dólares, y nosotros, en vez de esperar, o quedarnos quietos, nos pusimos a comprar local industrial, a importar maquinaria, es decir, nos excedimos en nuestros cálculos económicos financieros y no previmos un problema grave que se venía en el país, que fue la devaluación del dólar, en el año 1982, con la famosa “tablita”. Nuestro compromiso con las nuevas inversiones, fueron en moneda extranjera, y hasta que la fábrica comenzó a funcionar nuevamente, nos agarró de lleno en el año 82, con la devaluación. Esto nos desfinanció, por eso digo que nos apresuramos en reinvertir, como lo hicimos. A partir de allí Nibo Plast trató de sobrevivir, y cómo sobrevivimos tantos años, es una pregunta que no tiene respuesta.
Marzo 2006 / Montevideo - Uruguay
Volver a Entrevistas
|