Una empresa líder en almacenaje y dosificación de Plásticos.
Entrevista al Ing. Romualdo Tellería, Director General de Silos y Camiones, S.A. de C.V.
Volver a Entrevistas
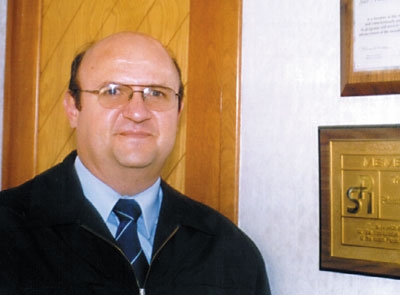
La siguiente entrevista, realizada en la planta de Silos y Camiones, en Pachuca, México, nos da una visión sobre una temática tan importante y vital para la industria actual, como lo es el almacenaje y cuidado de materias primas, su transporte y dosificación a maquinarias, y el uso de equipos periféricos, con el fin de mejorar la calidad y ahorrar en las líneas productivas..
¿Cómo inicia el Grupo Industrial Tellería?
El Grupo comienza su actividad local con la llegada a México, de mi abuelo en 1903. Inmediatamente se instala en Pachuca, ciudad que tenía como primer negocio del desarrollo de su economía, a la industria minera. Comienza a trabajar en una Casa de venta de todo tipo de productos, y es allí donde se especializa en el área de ferretería. Al comenzar su actividad propia, lo hace en forma importante con la venta de arados, (hoy símbolo en nuestro logo). Cuando fallece, mi padre ocupa su lugar, y ya para esa época, se habían instalado cerca de cuarenta ferreterías, en dónde se proveía a la industria de la construcción. Debido a que uno de los temas de la ferretería era vender y mover el cemento, se comienza a introducir en el tema del transporte. En ese entonces, se desperdiciaba mucho cemento en las cargas y descargas, ya que frecuentemente los sacos de material se rompían, hecho que además traía connotaciones graves de salud para los cargadores que respiraban esa contaminación ambiental. Ya desde 1968, movilizábamos 2.000 toneladas diarias de cemento, pero en esa época, y en plena crisis del papel, las roturas en promedio significaban, aproximadamente, una cada veinte bolsas. Imagina la dimensión del problema de contaminación por rotura. Es allí que mi padre, estudia como mejorar las condiciones humanas de carga y transporte de este producto, y de ello nace Silos y Camiones, en esa búsqueda de solucionar el problema de la contaminación por roturas de los sacos de cemento.
Así la empresa, comienza su crecimiento y su especialización en fabricación de silos para almacenaje. Se empezó el desarrollo de camiones, empezando para 17 toneladas, para el manejo de materiales, y silos de 30 toneladas. Lentamente, estos vehículos comenzaron a ser requeridos y adquiridos por la industria de la construcción, y en particular la del cemento.
Recién para el año 1974, produjimos la primera línea de silos, para utilización de plásticos, fue en la ciudad de Atlacomulco. Eran silos para almacenar polipropileno, importado de Houston Texas, que era transportado por ferrocarril. A su vez, habíamos resuelto el problema de la descarga de ese PP, instalando silos atornillados que descargaban desde la espuela del ferrocarril. Succionábamos en el auto tanque, y de allí lo dirigíamos a los silos para alimentación de las máquinas, que fabricaban sacos de rafia, utilizado para la industria azucarera y del fertilizante.
Luego de la crisis de 1976, debido a una devaluación fuerte en México, decae la industria del cemento debido al estancamiento de la construcción. Sin embargo, nos mantuvimos constantes y sobrepusimos esta problemática, gracias a la industria del plástico que ya era parte de nuestro mercado. Otra de las compañías del Grupo que crece con esta evolución, es Transportes Tellería. También comienza por el tema de construcción, relacionado a la movilización de cargas muy pesadas, siendo hoy día la compañía más grande en manejo de materiales de carga voluminosa en México. Recientemente incorporamos al Grupo, una imprenta offset, en dónde brindamos servicios a terceros y por supuesto atiende nuestros requerimientos.
¿Que implica almacenar las materias primas en silos?
La ventaja de un sistema a granel, es básicamente el ahorro en el costo de la materia prima y por supuesto, el cuidado de la misma. Es el almacenamiento en sí, es decir, antes se almacenaban sacos, que requiere mucho espacio, además de condiciones especiales de cuidado. Luego se producían las roturas en almacén, roturas en el transporte a la producción, humedad, suciedad, etc. El ubicar la materia prima en silos, un almacenamiento vertical, esto implica que con poco espacio se puede guardar mucha capacidad. Hoy en día, y no solamente en México, el área de espacio es muy importante (y muy cara), es pues un almacenamiento adecuado y una ventaja competitiva.
Con el transcurso del tiempo, las industrias han ido creciendo y se han ido desarrollando, siendo el silo, parte fundamental en ese desarrollo, dándole entre otras cosas, muchas ventajas en lo que refiere a la calidad, ya que se evita con estos sistemas, la contaminación de la materia prima, por roturas de los sacos y/o la mala manipulación de los operarios.
Respecto a lo que refiere a la transportación de las materias primas en silos/remolque, es un sistema completamente controlado y cerrado, no hay contaminación del material. No lo carga la gente, es todo automatizado, donde se sopla el material por el conducto hacia los silos de almacenamiento. Entre otras cualidades, el sistema es más sano para el operario, que evita las cargas y descargas de materiales pesados, ya que un saco de plástico no pesa menos que 25 kilos. Así que el vacío o la presión son una solución más productiva que la fuerza bruta, de hecho tenemos un concepto, “no lo cargue, sóplelo”.
¿Cuál es el criterio para el diseño de los silos?
Tenemos variedad y diseñamos a la necesidad del cliente, podemos fabricarlo para capacidades desde cinco toneladas hasta más de mil toneladas. Por otra parte, las características del silo, dependen del uso y del tiempo de carga. Hay silos que se cargan una vez al mes, otros que los cargan cada 2 horas, está relacionado dependiendo del proceso de carga y descarga. Por ejemplo, un camión trae 30 toneladas, y se consumirán en una semana, esto implica un pasaje de esas toneladas por los silos en ese tiempo, entonces, requieren protecciones internas ya sea de pintura o del material en sí, que tolere ese movimiento de fricción del material.
Adicional a esto, elaboramos a medida del cliente la automatización que va a necesitar, cuales son sus variables de control, ya que cada dosificación de las maquinas es diferente, tanto en el porcentaje como en la precisión que necesitan, por ejemplo la industria farmacéutica requiere mucha exactitud. Entonces dependiendo de las variables, seleccionamos equipos mas finos, de más control, que normalmente desgraciadamente se van a mayor precio, o por otro lado, controles más estándar a base de volumétricos de tornillos.
Por otra parte, el diseño para la fabricación depende de los lugares donde se vayan a instalar. Si es una zona de alta corrosión como es el mar, nosotros recomendamos silos de aluminio o de acero inoxidable. Si es una zona sísmica fuerte, el acero inoxidable es más apropiado que el aluminio, si es una zona sísmica baja, el aluminio es el ideal por el costo que es más barato que el acero inoxidable. Entonces dependiendo de varios factores, hacemos combinaciones entre aluminio, acero de carbón, pintados con epóxy o acero inoxidable.
¿Sobre el manejo de materias primas?
Nuestros silos remolques llevan 30 toneladas, pero si son contenedores normalmente traen 20 toneladas, para este caso lo que usamos es un liner interior, que es una bolsa de plástico que cubre o forra todo el interior, en el cual te permite llenarlo de materia prima y que no se contamine.
El problema de los contenedores, es que no tienen la descarga para presurizar y descargarlos. Tenemos que voltear el contenedor para enviar a todo el material a un punto trasero y de ahí succionarlo para dirigirlo a los silos. Dependiendo de la distancia que se tiene que mandar el material, desde el lugar donde estamos descargando hasta los silos, es la capacidad del soplador que necesitamos poner. No es lo mismo descargar 10 toneladas por hora, de un contenedor que esta cerca de los silos, que si queremos descargar un contenedor que esta a 100 metros.
Por otra parte en el manejo de materiales a granel, la altura sobre el nivel del mar es muy importante. El aire en el nivel del mar es mucho más pesado que en zonas elevadas, entonces los colectores de polvo que se necesitan para el manejo, por ejemplo del PVC, o del SAN, o de cualquier material plástico polvoriento, son mucho mas grandes en las ciudades altas, que en las ciudades bajas. Como anécdota, te cuento que en Baja California, tenemos equipos que están a 50 metros bajo nivel del mar, funcionando en forma perfecta!
¿Cómo controlamos los inventarios de materias primas?
Para el control de inventario del silo, tenemos dos sistemas principales de medición, uno es el de distancia, ya sea éste, ultrasonido o todos los equipos que miden la diferencia desde la tapa hasta donde está el material. Otro sistema es el de básculas, que se usan tanto en camiones como en los silos. Los sistemas de medición, permiten controlar la cantidad de materias primas que circulan en el circuito; del camión cisterna a silos, al proceso productivo (mezcladores, secadores, etc.,) y por último a las máquinas. Aquí se puede medir, cuanto material se consume, y a que máquinas se ha dirigido, logrando de esta manera, un acumulado en la computadora, donde se va registrando el consumo de cada máquina del material. Esto nos ayuda a medir productividades, incluso podemos llevar un historial de cada hora, cuanto material se esta consumiendo y así poder detectar si se paró o no la máquina, realmente puedes controlar. Hoy la tecnología de computación en el control estadístico y de productividad es increíble, y lo importante es que el cliente puede detectar lo que quiere. La industria del plástico, lentamente y con mucho trabajo, fue asumiendo toda esta realidad y se dio cuenta de los enormes beneficios de aplicar la tecnología de silos y alimentación automática. Anteriormente, y con demasiado esfuerzo, había que convencer y explicar planta por planta, pero hoy la gente te habla por iniciativa propia para poner silos, ya es una cultura de los últimos 2 ó 3 años. Sin embargo, aún hay países que definitivamente no han madurado en este aspecto.
Respecto al almacenaje de plásticos...
En el área del plástico, hay muchos y diferentes materiales que deben ser tratados de distintas maneras. Por ejemplo, el PVC, uno de nuestros mercados más importantes, es un material de polvo que se mezcla y se hacen compuestos para luego entrar en proceso. En todo el manejo interviene lo que es la recolección de polvo y las dosificaciones precisas de químicos.
Los polietilenos y los polipropilenos, son materiales muy nobles, porque son muy limpios. Aquí lo que se necesita es dosificar en el momento y la cantidad adecuada. Durante 24 horas se estará surtiendo a las máquinas, sin complicaciones. La ventaja es que no son corrosivos ni abrasivos, entonces no tienes mayores problemas, paredes bien tratadas tienen una duración de muchos años, con cero contaminación. Tenemos silos en el mercado desde 1974 y hoy lo siguen operando exactamente igual sin necesidad de tener que darle un mantenimiento.
Pero en los casos de materiales que son más abrasivos, ya sea por que son más rígidos a la hora de moverlo en forma neumática, el recubrimiento debe ser más potente, aquí hablamos de 10 ó 12 años para un mantenimiento. Por ejemplo para el caso del PET, otro de nuestros mercados importantes, utilizamos un recubrimiento que es de los más caros, realizando una similitud a lo que es la resina de aluminio de acero inoxidable.
¿Respecto el control de humedad en el almacenaje?
En este tema, depende del tipo de material que se almacene y que requerimiento necesite. Tenemos los silos que se ventean a la atmósfera y que puede entrar o salir el aire libremente, tenemos silos que le ponemos un sistema controlado de aire seco humificado, y tenemos otro sistema donde al mismo aire del soplador lo tratamos antes de usar la descarga y dentro del silo controlamos la humedad. En el caso de los plásticos que son higroscópicos, por ejemplo todos los que llevan pigmentos de negro de humo, o algunos plásticos como el PET, que deben secarse a fuerza en un secador para que se le quite toda la humedad antes de llegar a la máquina, entonces a los silos no se les pone ningún tratamiento de aire. En los casos que necesitamos evitar el 100% de humedad, ponemos un equipo para que constantemente esté circulando aire seco. Sobre todo al existir cambios drásticos de temperatura, por ejemplo cuando tenemos un sol fuerte, tenemos una temperatura de 28 o más grados y luego al atardecer desciende a 14 grados, produciendo un cambio de temperatura que suda los silos, y si hay aire que tiene humedad relativa alta, pues esa misma humedad se precipita y moja el material. Por eso una solución es el silo de doble tapa, que tiene una recamara y crea un colchón interno protector. También realizamos recubrimientos de poliuretano espumado en el exterior para protegerlo contra esos cambios de humedad y recomendamos en algunos casos, que los silos estén dentro de una estructura, de una nave, para tener doble techo.
¿Exportación?
Comenzamos nuestras exportaciones en 1976, enviando silos a República Dominica. Fue recién a partir del 95, dónde enfocamos la exportación como algo más constante. Empezamos a participar en la NPE, donde detectamos la necesidad de estar presentes, no tanto para el mercado americano, pero sí para los empresarios latinoamericanos que la visitan en cada edición. Por otra parte, somos asociados de la SPI, (Society of the Plastics Industry), organizador del evento, en la cual, nos han dado mucha información tanto comercial como técnica, y por supuesto las ventajas para ser expositor en la NPE.
Hoy en día, el 70% de nuestras exportaciones, representan productos para la industria plástica, una industria muy noble. Nuestro mercado importante de exportación es Latinoamérica completa, salvo alguna Guyana, el resto de los países tienen productos de Silos y Camiones.
¿Sobre equipos periféricos?
En México tenemos la distribución de varios equipos periféricos, como por ejemplo Bindicator que es una de las más grandes compañías de indicadores de nivel. La tenemos en forma exclusiva para este mercado, y para todo lo que es Latinoamérica. Después tenemos secadoras de plástico, las mezcladoras de producto y de pigmentos, todo lo que es el equipo de recuperación y de transporte de baja capacidad.
Manejamos la marca Pelletron, que también tenemos la representación para todo Latinoamérica, que son especiales para la eliminación de todo tipo de partículas extrañas, es decir, todo lo que es la limpieza del pellet. Es un sistema de diseño de trampas, con bobinas magnéticas, en el cuál cambia la polaridad y repele al plástico de las partículas contaminantes, y luego a base de aire, logramos limpiar perfectamente todo el material. De esta manera se evita, la incursión a las máquinas, por ejemplo de materiales ferrosos, que van a quedar aprisionados en esas trampas.
Tenemos equipos para descarga de ferrocarril, ya sea si el cliente tiene una espuela dentro de la fábrica, o no. Realizamos una descarga por gravedad y otra presurizada. En el caso de la descarga presurizada le inyectamos con soplador de aire, dentro de la unidad y por presión mandamos a los silos. En el caso de la descarga por gravedad, tomamos de la parte de abajo el plástico, lo succionamos a un equipo que le llamamos succión-presión, y después de la succión, por presión lo mandamos a los silos. Fabricamos nuestras propias tolvas semi-remolques, para el manejo de plástico a granel, que cargan directamente de las petroquímicas.
¿Su sistema de calidad?
Empezamos en 1997, con lo que refiere a la temática de las normas de calidad. Debido a la demanda que teníamos en exportación, particularmente con compañías europeas, nos interiorizamos en el tema de normalización y obtuvimos las ISO 9000. A partir de allí, hemos formado un grupo de mejora continua, grupos de desarrollo e investigación y un sistema de control de proceso y del ciclo productivo, es decir, un desarrollo constante enfocado a poner mucho más énfasis en el servicio al cliente y en el proceso integral. En la actualidad, ya estamos certificando las normas ISO 2000. Hemos avanzado mucho en lo que es Intranet e Internet, en todo lo que es el proceso de calidad mismo. Desde hace dos años, comenzamos un centro de desarrollo tecnológico, para investigación aplicada. Realizamos investigaciones para el cliente que solicita un proyecto determinado para sus productos. Instrumentamos varios tipos de ensayos, y además fabricamos equipos pilotos en nuestra planta para realizar una metodología a escala. En la actualidad, damos cursos de capacitación para nuestros clientes, enseñándoles el concepto del proceso y como poner un sistema de manejo, todo esto antes de montar la planta.
¿Para finalizar?
Silos y Camiones empezó siendo una Empresa de manejo de materiales a granel, hoy ya nuestra filosofía y nuestro objetivo, es de estar enfocados hacia como ayudar al cliente en reducir sus costos, para que puedan estar en los mercados en forma más competitiva.
Muchas Gracias
Pachuca - México - 28/11/ 2003
Fotografias; Rev. Ingenieria Plástica
Volver a Entrevistas
|